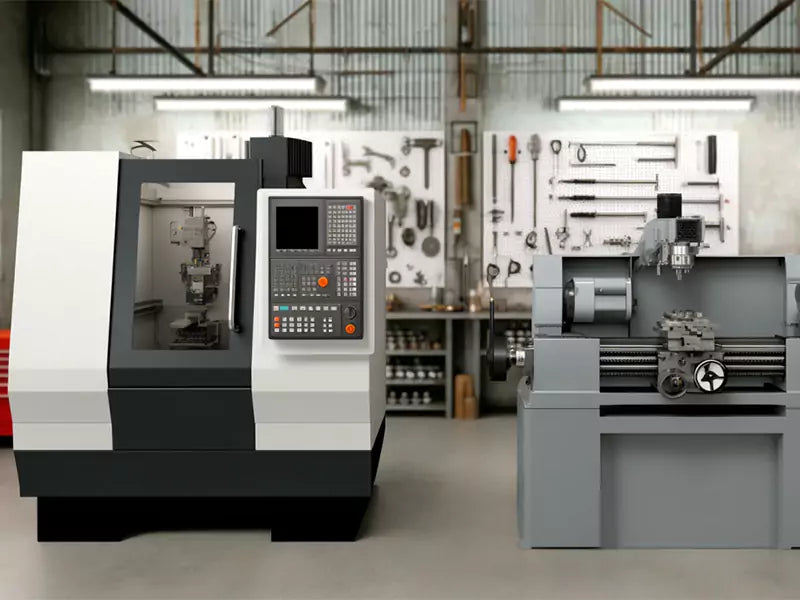
The Evolution of CNC Machines: From Manual to Digital Precision
The journey of manufacturing has been nothing short of revolutionary, with Computer Numerical Control (CNC) machines playing a pivotal role in this transformation. From the early days of manual machining to today’s digital precision, CNC machines have continually evolved, enhancing efficiency, accuracy, and productivity. This blog delves into the fascinating evolution of CNC machines, exploring their history, advancements, and the significant impact they’ve had on modern manufacturing.
The Birth of Manual Machining
Before CNC machines, manual machining was the norm. Skilled machinists operated lathes, milling machines, and grinders by hand, using their expertise to produce parts with a reasonable degree of accuracy. This process, though effective, was labor-intensive, time-consuming, and prone to human error. Every part required meticulous attention to detail, and replicating complex designs was a challenging task.
The Advent of Numerical Control
The concept of Numerical Control (NC) emerged in the late 1940s and early 1950s, marking a significant leap forward in machining technology. John T. Parsons and his team developed the first NC machine, which used punched tape to control the movements of a milling machine. This innovation allowed for more precise and repeatable operations, reducing the reliance on manual labor.
NC machines used a series of coded instructions to control the movement of machine tools. These instructions, often stored on punched cards or magnetic tapes, guided the machine’s actions, ensuring consistent and accurate results. Although revolutionary, early NC machines were limited by the complexity of the coding process and the rigidity of the hardware.
The Rise of Computer Numerical Control (CNC)
The real game-changer in machining came with the advent of Computer Numerical Control (CNC) in the 1970s. CNC machines integrated computer technology with numerical control, allowing for greater flexibility, automation, and precision. Unlike their NC predecessors, CNC machines could interpret complex digital instructions, making it possible to produce intricate designs with minimal human intervention.
CNC technology utilized a central computer to control the machine’s movements, interpreting digital instructions known as G-codes and M-codes. These codes dictated the machine’s actions, such as tool changes, spindle speeds, and cutting paths. The introduction of CNC software enabled machinists to design parts using Computer-Aided Design (CAD) software and convert those designs into machine-readable instructions through Computer-Aided Manufacturing (CAM) software.
Advancements in CNC Technology
The evolution of CNC machines has been marked by continuous advancements, each contributing to improved performance and capabilities. Some of the key developments include:
- Multi-Axis Machining: Early CNC machines operated on three axes (X, Y, and Z). Modern CNC machines can operate on up to five or more axes, allowing for the production of highly complex and intricate parts. Multi-axis machining has revolutionized industries such as aerospace and automotive, where precision and complexity are paramount.
- High-Speed Machining: Advances in spindle technology, cutting tools, and control systems have enabled CNC machines to achieve higher cutting speeds and feed rates. High-speed machining reduces production times, increases efficiency, and enhances the quality of finished parts.
- Integrated Automation: The integration of automation technologies, such as robotic arms and pallet changers, has further enhanced the capabilities of CNC machines. Automated systems can handle tasks such as tool changes, part loading and unloading, and quality inspection, reducing the need for manual intervention and increasing overall productivity.
- Real-Time Monitoring and Feedback: Modern CNC machines are equipped with sensors and monitoring systems that provide real-time feedback on machine performance. This data allows for predictive maintenance, reducing downtime and ensuring optimal machine operation.
- Additive Manufacturing: The advent of additive manufacturing, or 3D printing, has expanded the possibilities of CNC technology. Hybrid machines that combine additive and subtractive manufacturing capabilities can produce complex parts with a high degree of accuracy and efficiency.
The Impact of CNC Machines on Manufacturing
The evolution of CNC machines has had a profound impact on the manufacturing industry. Some of the most notable benefits include:
- Increased Precision and Accuracy: CNC machines can produce parts with extremely tight tolerances, ensuring consistent quality and reducing the need for manual inspection and rework.
- Enhanced Productivity: Automation and high-speed machining capabilities have significantly increased production rates, allowing manufacturers to meet demanding deadlines and stay competitive in the global market.
- Cost Savings: While the initial investment in CNC machines can be substantial, the long-term cost savings are significant. Reduced labor costs, minimized material waste, and improved efficiency contribute to lower overall production costs.
- Design Flexibility: CNC machines can easily adapt to produce a wide range of parts, from simple components to complex geometries. This flexibility allows manufacturers to respond quickly to changing customer demands and market trends.
- Improved Safety: CNC machines reduce the need for manual intervention, minimizing the risk of workplace accidents and injuries. Advanced safety features, such as automatic shutoff and collision detection, further enhance operator safety.
The Future of CNC Machining
The evolution of CNC machines is far from over. As technology continues to advance, we can expect further innovations that will push the boundaries of what is possible in manufacturing. Some of the trends shaping the future of CNC machining include:
- Artificial Intelligence and Machine Learning: AI and machine learning algorithms can optimize machining processes, predict maintenance needs, and improve overall efficiency. These technologies will enable CNC machines to become smarter and more autonomous.
- Internet of Things (IoT): IoT connectivity allows CNC machines to communicate with other devices and systems, enabling seamless integration with smart factories and Industry 4.0 initiatives. Real-time data sharing and analysis will enhance decision-making and operational efficiency.
- Advanced Materials: The development of new materials, such as composites and advanced alloys, will require CNC machines to adapt and evolve. Machines capable of handling these materials will open up new possibilities in industries such as aerospace, medical, and automotive.
- Sustainability: As environmental concerns become more pressing, CNC machines will need to incorporate sustainable practices. Energy-efficient designs, reduced material waste, and the use of eco-friendly materials will become increasingly important.
- Human-Machine Collaboration: The future of CNC machining will likely involve closer collaboration between humans and machines. Augmented reality (AR) and virtual reality (VR) technologies can assist operators in programming and monitoring CNC machines, enhancing productivity and reducing errors.
Conclusion
The evolution of CNC machines, from manual machining to digital precision, has transformed the manufacturing industry. These machines have revolutionized the way we produce parts, offering unparalleled accuracy, efficiency, and flexibility. As technology continues to advance, the future of CNC machining holds even greater promise, with innovations that will further enhance our capabilities and drive the industry forward. Embracing these advancements will be key to staying competitive in an ever-evolving global market, ensuring that CNC machines remain at the forefront of modern manufacturing.