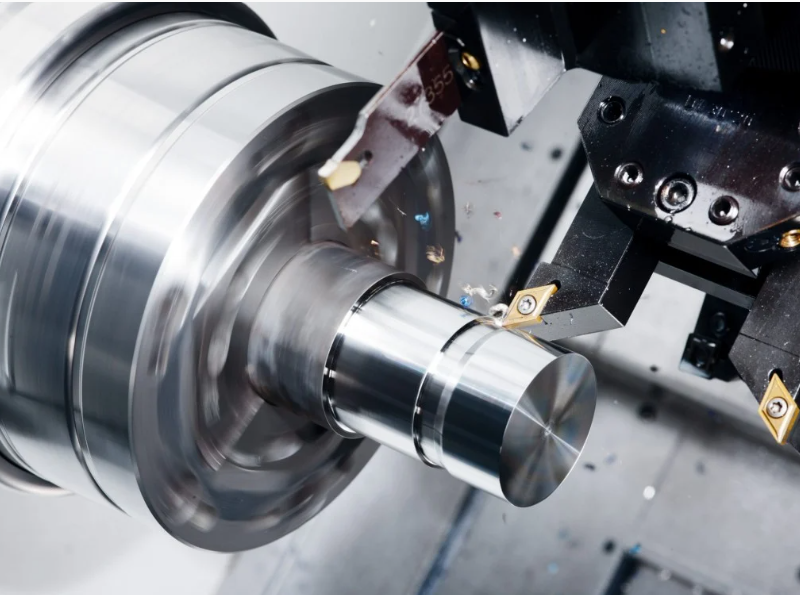
CNC TURNING AND CNC TURNING CENTER BASICS
Introduction to CNC Turning
If you’ve been in manufacturing, engineering, or are an avid tech enthusiast, chances are you’ve heard about CNC turning. But what exactly is it? CNC (Computer Numerical Control) turning is a subtractive machining process where a cutting tool removes material from a rotating workpiece to create a desired shape. This process is pivotal in the manufacturing industry for producing precise and intricate components. From aerospace to automotive, CNC turning has revolutionized how parts are made, ensuring consistency, efficiency, and high-quality output.
In this blog post, we will explore the basics of CNC turning and CNC turning centers. We’ll take you through its fundamental processes, the advantages it offers, and how to select the right CNC turning center for your needs. We’ll also touch on future trends that are set to reshape the landscape of CNC turning. By the end of this post, you’ll have a comprehensive understanding of CNC turning and its crucial role in modern manufacturing.
Fundamentals of CNC Turning
Overview of the CNC Turning Process
CNC turning begins with a cylindrical workpiece, usually made of metal or plastic, which is secured onto a lathe. The lathe then rotates the workpiece at high speeds while a cutting tool, controlled by computer software, moves along the workpiece to remove material. The precision of the cutting tool’s movements allows for the creation of complex shapes and features, from simple cylindrical forms to intricate geometries.
The process involves several key steps:
- Programming: A computer program, often written in G-code, dictates the movements of the cutting tool.
- Setup: The workpiece is securely clamped onto the lathe, and the cutting tool is positioned.
- Machining: The lathe spins the workpiece while the cutting tool removes material to achieve the desired shape.
- Finishing: Additional processes like polishing or coating may be applied to enhance the part’s surface quality.
Key Components of a CNC Turning Center
A CNC turning center is a sophisticated machine equipped with several vital components that work in harmony to perform turning operations. The primary components include:
- Lathe Bed: The base of the machine that supports all other components.
- Spindle: Holds and rotates the workpiece at varying speeds, essential for different machining operations.
- Turret: Houses multiple cutting tools and can be indexed to bring the required tool into position.
- Control Panel: The interface where operators input commands and monitor the machine’s performance.
- Tailstock: Provides additional support for longer workpieces, ensuring stability during machining.
Types of CNC Turning Operations
CNC turning isn’t limited to just one type of operation. Various techniques can be employed to achieve different results:
- Facing: The cutting tool moves perpendicularly to the workpiece’s axis, creating a flat surface at the end.
- Parting: Used to cut off a finished part from the remaining material.
- Threading: Involves cutting screw threads into the workpiece.
- Drilling: A drill bit is used to create holes in the workpiece.
- Boring: Enlarging an existing hole to achieve greater accuracy or a specific diameter.
Advantages and Applications
Benefits of Using CNC Turning Machines
CNC turning machines offer numerous advantages that make them indispensable in modern manufacturing:
- Precision and Accuracy: CNC systems can achieve tolerances within micrometers, ensuring parts meet exact specifications.
- Efficiency: Automation reduces human error and allows for continuous operation, increasing productivity.
- Flexibility: Easily switch between different operations and materials, accommodating various production needs.
- Consistency: Every part produced is identical, maintaining quality standards.
- Cost-Effective: Reduced waste and faster production times result in lower overall costs.
Real-World Applications in Different Industries
CNC turning finds applications across various industries due to its versatility and precision:
- Aerospace: Manufacturing engine components, landing gear parts, and structural elements.
- Automotive: Producing gears, shafts, and brake components.
- Medical: Creating surgical instruments, implants, and prosthetics.
- Electronics: Fabricating connectors, housings, and heat sinks.
- Consumer Goods: Crafting high-quality kitchenware, jewelry, and sporting equipment.
CNC Turning Center Selection Guide
Factors to Consider When Choosing a CNC Turning Center
Selecting the right CNC turning center is crucial for optimizing your manufacturing processes. Here are some factors to consider:
- Material Compatibility: Ensure the machine can handle the types of materials you work with, be it metals, plastics, or composites.
- Size and Capacity: Choose a machine that accommodates the size of your workpieces and the volume of production.
- Precision Requirements: Different projects demand varying levels of precision; select a machine that meets your accuracy needs.
- Ease of Use: User-friendly interfaces and programming capabilities can significantly impact productivity.
- Support and Maintenance: Consider the availability of technical support, maintenance services, and the cost of spare parts.
Popular CNC Turning Center Brands and Models
Several reputable brands offer high-quality CNC turning centers. Here are a few popular ones:
- Mazak: Known for its innovative designs and reliable performance.
- Haas: Offers a range of versatile and user-friendly machines.
- DMG Mori: Renowned for precision engineering and advanced technology.
- Okuma: Combines robust construction with high-speed capabilities.
- Doosan: Provides cost-effective solutions with excellent durability.
Future Trends in CNC Turning
Innovations and Technological Advancements
The field of CNC turning is continuously evolving, with several exciting advancements on the horizon:
- Smart Manufacturing: Integration of IoT (Internet of Things) for real-time monitoring and predictive maintenance.
- AI and Machine Learning: Enhancing automation and optimizing machining processes through data analysis.
- Additive Manufacturing: Combining CNC turning with 3D printing for hybrid manufacturing solutions.
- Advanced Materials: Exploring the use of new materials like carbon fiber composites and superalloys.
- Sustainability: Developing eco-friendly machining processes to reduce environmental impact.
Predictions for the Future of CNC Turning in Manufacturing
Looking ahead, CNC turning is set to become even more integral to the manufacturing industry:
- Increased Automation: Greater reliance on fully automated systems to boost efficiency and reduce labor costs.
- Customization: Enhanced ability to produce customized parts on-demand, catering to specific customer requirements.
- Global Competition: Continued advancements in technology will drive global competition, pushing manufacturers to adopt cutting-edge solutions.
- Collaboration: Increased collaboration between human operators and machines, leveraging the strengths of both.
- Regulatory Compliance: Stricter regulations on quality and sustainability will shape the development of future CNC turning technologies.
Conclusion
CNC turning has undeniably transformed the landscape of modern manufacturing, offering unparalleled precision, efficiency, and versatility. From aerospace to automotive, its applications are vast and varied, making it a critical tool for industries worldwide.
Understanding the fundamentals of CNC turning and selecting the right turning center can significantly impact your manufacturing processes. By staying informed about future trends and innovations, you can ensure your business remains competitive in an ever-evolving market.
Ready to take the next step in optimizing your manufacturing operations? Explore further resources and consider integrating CNC turning into your workflow to experience its numerous benefits firsthand.