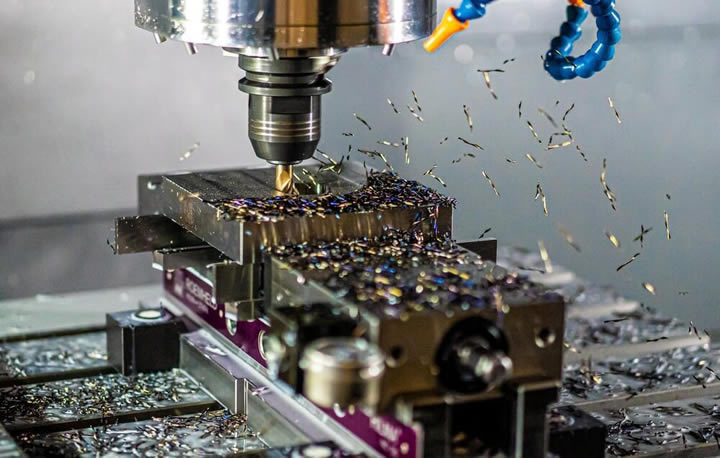
CNC Cutting Tools Overheating: What You Need to Know
The Crucial Role of CNC Cutting Tools in Modern Manufacturing
CNC cutting tools are the backbone of modern manufacturing. These advanced machines enable precision cutting of materials, ensuring high-quality and efficient production. For manufacturing professionals and CNC operators, understanding how these tools work and how to maintain them is vital to achieving optimal performance.
What Happens When CNC Cutting Tools Overheat?
Overheating in CNC cutting tools is a common issue that can significantly impact the manufacturing process. When cutting tools get too hot, it can lead to premature wear, reduced tool life, and even damage to the workpiece. This section will explore the mechanisms behind overheating and why it’s a problem worth addressing.
The Fallout of Overheating: Tool Life and Workpiece Quality
When CNC cutting tools overheat, it affects both the tool and the workpiece. The tool’s lifespan shortens as it wears out faster, leading to increased costs for replacements. Additionally, the quality of the workpiece suffers, with potential issues like surface burns, dimensional inaccuracies, and compromised structural integrity.
Why Do CNC Cutting Tools Overheat?
Several factors contribute to the overheating of CNC cutting tools. Understanding these causes is the first step in preventing and managing the issue.
Material Properties
The type of material being cut plays a significant role in overheating. Harder materials generate more heat during the cutting process.
Cutting Speed and Feed Rate
Incorrect cutting speeds and feed rates can cause excessive friction and heat build-up. Adjusting these parameters is crucial to maintaining optimal tool temperature.
Coolant Application
Inadequate or improper use of coolant can lead to overheating. Coolants help dissipate heat and reduce friction, so their correct application is essential.
Strategies to Prevent and Manage Overheating
Preventing overheating is key to extending the life of your CNC cutting tools and ensuring high-quality workpieces.
Regular Maintenance
Routine maintenance checks can help identify potential overheating issues before they become significant problems. Inspections should include checking for wear and tear on the tools and ensuring that all cooling systems are functioning correctly.
Optimize Cutting Parameters
Adjusting cutting speeds and feed rates to suit the material and tool can significantly reduce heat generation. Using manufacturer-recommended settings is a good starting point.
Effective Coolant Systems
Ensure that the coolant is applied correctly and consistently during the cutting process. Regularly check and maintain the coolant system to prevent overheating.
Real-World Solutions to Overheating Issues
With practical examples and case studies, we can learn effective methods to manage and prevent overheating in CNC cutting tools.
Case Study 1: Automotive Industry
In the automotive industry, overheating of cutting tools can lead to dimensional inaccuracies in engine components. By implementing optimized cutting parameters and advanced coolant systems, manufacturers have successfully reduced overheating issues.
Case Study 2: Aerospace Manufacturing
Aerospace components require high precision, and overheating can compromise safety. Through regular maintenance and the use of high-quality coolants, aerospace manufacturers have managed to keep overheating at bay.
Case Study 3: Small-Scale Manufacturing
Even small-scale manufacturers face overheating issues. A case study showed that by simply adjusting feed rates and ensuring proper coolant flow, a small workshop significantly improved tool life and workpiece quality.
Putting It All Together for a Cooler, More Efficient Operation
Understanding and managing overheating in CNC cutting tools is crucial for manufacturing success. By implementing regular maintenance, optimizing cutting parameters, and using effective coolant systems, you can extend tool life, reduce costs, and ensure high-quality workpieces.
For more tips on maintaining your CNC cutting tools and improving your manufacturing processes, stay tuned to our blog. If you have specific questions or need personalized advice, don’t hesitate to reach out to our team of experts.