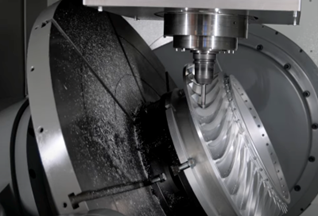
In today’s rapidly evolving manufacturing landscape, CNC machines have emerged as indispensable tools for precision engineering and efficient production. If you’re new to the world of manufacturing or considering a career in this field, understanding the basics of CNC (Computer Numerical Control) machines is essential.
In this comprehensive guide, we’ll explore the fundamentals of CNC machines, their types, components, operation, and applications. Whether you’re a novice enthusiast or an aspiring CNC programmer, this introductory guide will provide valuable insights into the fascinating realm of CNC machining.
Introduction to CNC Machines
CNC machines revolutionized manufacturing by automating the machining process through precise computer-controlled movements. Unlike traditional manual machining, where operators manually control the cutting tools, CNC machines execute programmed commands to achieve unparalleled accuracy and repeatability. This automation not only enhances productivity but also enables the production of complex parts with intricate geometries.
Types of CNC Machines
CNC (Computer Numerical Control) machines have transformed manufacturing processes by offering unparalleled precision, efficiency, and versatility. Among the various types of CNC machines, CNC milling machines, turning machines (lathes), vertical machining centers (VMCs), horizontal machining centers (HMCs), and drilling and tapping centers (DTCs) are prominent.
CNC machines come in various configurations, each tailored to specific machining tasks. Some of the most common types include:
CNC Milling Machines: These versatile machines employ rotating cutting tools to remove material from a workpiece, producing flat or contoured surfaces with high precision. CNC milling machines are renowned for their versatility. They utilize rotating cutting tools to remove material from a workpiece, resulting in flat or contoured surfaces with exceptional precision. Whether it’s creating intricate designs or producing precise components, CNC milling machines excel in a wide range of applications.
CNC Turning Machines (Lathes): Used primarily for cylindrical parts, CNC lathes rotate the workpiece while a stationary cutting tool shapes it into the desired form. CNC turning machines, also known as lathes, specialize in machining cylindrical parts. The workpiece rotates while a stationary cutting tool shapes it into the desired form. This process is ideal for producing shafts, pins, and other cylindrical components with high accuracy and repeatability.
CNC Vertical Machining Centers (VMCs): VMCs feature a vertical spindle orientation, making them ideal for milling, drilling, and tapping operations on three-dimensional workpieces. Vertical machining centers (VMCs) feature a vertical spindle orientation, making them well-suited for milling, drilling, and tapping operations on three-dimensional workpieces. With their ability to handle complex geometries and multi-axis machining, VMCs are indispensable in various industries, including aerospace, automotive, and mold making.
CNC Horizontal Machining Centers (HMCs): HMCs have a horizontal spindle orientation, facilitating efficient machining of large or heavy parts from multiple angles. Horizontal machining centers (HMCs) offer a horizontal spindle orientation, enabling efficient machining of large or heavy parts from multiple angles. This configuration enhances accessibility and facilitates the production of components with intricate features and tight tolerances.
CNC Drilling and Tapping Centers (DTCs): These specialized machines excel at drilling, tapping, and other hole-making operations, offering high-speed and precision for component production. Drilling and tapping centers (DTCs) specialize in hole-making operations, including drilling, tapping, and reaming. These machines deliver high-speed and precision, making them indispensable for component production in industries such as electronics, telecommunications, and automotive.
In summary, CNC machines play a pivotal role in modern manufacturing, offering unparalleled capabilities in terms of precision, efficiency, and versatility. From milling and turning to drilling and tapping, each type of CNC machine serves unique purposes and contributes to the seamless production of high-quality components across various industries.
Components of CNC Machines
A typical CNC machine comprises several key components, each playing a crucial role in its operation:
Control Unit: The brain of the CNC system, responsible for interpreting the programmed instructions (G-code) and orchestrating the machine’s movements.
Machine Tool: The physical structure housing the cutting tools, workpiece, and motion mechanisms, such as linear guides and ball screws.
Workpiece: The raw material or semi-finished part undergoing machining to achieve the desired shape and dimensions.
Cutting Tools: Various tools, including end mills, drills, inserts, and taps, mounted on the machine’s spindle to remove material from the workpiece.
Axes: CNC machines feature multiple axes (typically X, Y, and Z), which define the directions of movement for the cutting tool and workpiece.
CNC Programming
Programming is a critical aspect of CNC machining, where operators create instructions for the machine to follow. This process involves:
CAD/CAM Software: Designing the part geometry in Computer-Aided Design (CAD) software and generating toolpaths in Computer-Aided Manufacturing (CAM) software.
G-code Generation: Converting the toolpaths into machine-readable G-code, which comprises commands for tool movements, spindle speeds, feed rates, and coolant usage.
Simulation and Verification: Simulating the machining process to detect errors, collisions, or inefficiencies before executing the program on the actual machine.
Operation of CNC Machines
Operating a CNC machine requires proper setup, calibration, and monitoring to ensure optimal performance and part quality. The steps involved in CNC machining include:
Workpiece Setup: Securing the workpiece on the machine bed or fixture using clamps, vises, or other workholding devices.
Tool Setup: Installing and aligning the cutting tools in the machine’s spindle, ensuring proper tool length and tool-to-workpiece clearance.
Program Loading: Transferring the G-code program to the CNC machine’s control unit and verifying its integrity and compatibility.
Machining Execution: Initiating the machining process, monitoring the machine’s operation, and making adjustments as needed to maintain quality and efficiency.
Post-Processing: Inspecting the finished parts for dimensional accuracy, surface finish, and adherence to specifications, and performing any secondary operations if required.
Advantages of CNC Machining
CNC machining offers several distinct advantages over conventional manufacturing methods:
CNC (Computer Numerical Control) machining has revolutionized the manufacturing industry, offering a multitude of advantages over traditional machining methods. From enhanced precision to increased efficiency, CNC machining has become indispensable in various sectors. Let’s delve into the key advantages of CNC machining:
Precision: One of the most significant advantages of CNC machining is its exceptional precision. CNC machines operate with high accuracy, allowing for the production of parts with tight tolerances and intricate geometries. This precision ensures consistency and uniformity across all manufactured components, reducing the likelihood of errors or defects.
Efficiency: CNC machining significantly enhances productivity and efficiency compared to manual machining methods. Once programmed, CNC machines can operate continuously without the need for constant supervision, maximizing uptime and throughput. Additionally, CNC machines can perform complex machining operations in a fraction of the time it would take manually, resulting in faster turnaround times for production orders.
Automation: Automation is a cornerstone of CNC machining, enabling tasks to be performed with minimal human intervention. This automation not only reduces labor costs but also mitigates the risk of human error. CNC machines can execute pre-programmed instructions precisely, ensuring consistent quality and minimizing the need for rework or scrap.
Flexibility: CNC machines offer unparalleled flexibility in terms of production capabilities. They can easily switch between different machining operations, tooling configurations, and part geometries, making them suitable for a wide range of applications. Whether it’s prototyping, small-batch production, or high-volume manufacturing, CNC machines can adapt to varying production requirements with ease.
Complexity: CNC machining enables the production of highly complex parts and components that would be challenging or impossible to manufacture using conventional methods. With multi-axis machining capabilities and advanced CAD/CAM software, CNC machines can create intricate shapes, contours, and features with precision and repeatability. This capability opens up new possibilities for product design and innovation across industries.
Cost-Effectiveness: While the initial investment in CNC equipment may be substantial, CNC machining offers long-term cost savings over manual machining methods. The increased productivity, reduced labor costs, and minimized material wastage associated with CNC machining result in lower per-part costs and improved profitability in the long run.
Quality Control: CNC machining allows for stringent quality control measures throughout the manufacturing process. With real-time monitoring and feedback mechanisms, operators can identify and rectify issues promptly, ensuring that only parts meeting the highest quality standards are produced. This quality assurance is crucial, particularly in industries where precision and reliability are paramount, such as aerospace, medical, and automotive.
CNC machining offers a myriad of advantages that have transformed the manufacturing landscape. From precision and efficiency to automation and flexibility, CNC machines empower manufacturers to produce high-quality parts cost-effectively and at scale. As technology continues to evolve, the role of CNC machining in driving innovation and competitiveness across industries will undoubtedly become even more pronounced.
Applications of CNC Machines
CNC machining finds applications in diverse industries, including aerospace, automotive, medical, electronics, and consumer goods. Some common applications include:
Prototyping: Rapid prototyping of new product designs and concepts for validation and testing purposes.
Production Machining: High-volume manufacturing of precision components with tight tolerances and specifications.
Mold Making: Fabrication of injection molds, die molds, and tooling for plastic and metal casting processes.
Fabrication: Cutting, shaping, and finishing of sheet metal, tubing, and extrusions for various structural and decorative purposes.
Conclusion
In conclusion, CNC machines represent the pinnacle of modern manufacturing technology, enabling unprecedented levels of precision, productivity, and versatility. By understanding the basics of CNC machining, beginners can embark on a rewarding journey into the world of advanced manufacturing, equipped with the knowledge and skills to leverage this transformative technology effectively. Whether you’re an aspiring CNC programmer, machinist, or manufacturing enthusiast, mastering the fundamentals of CNC machines is essential for success in today’s competitive industrial landscape.