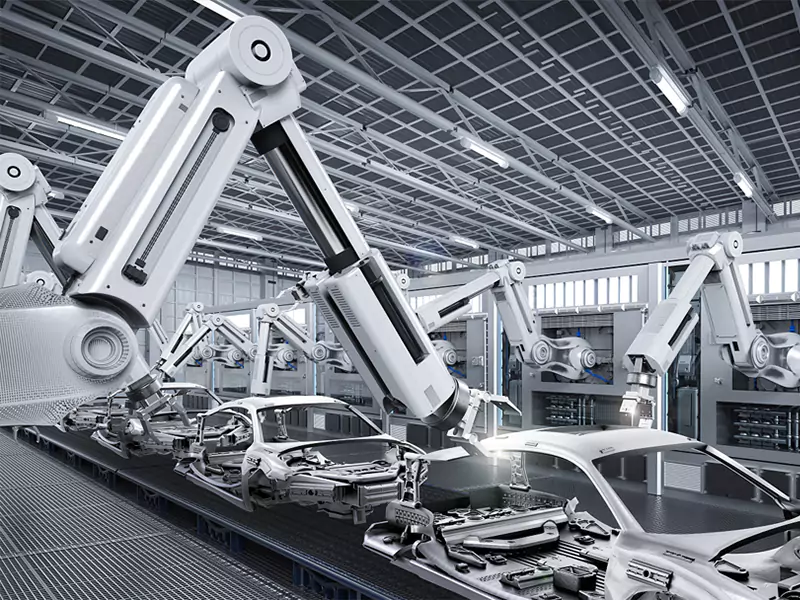
In today’s fast-paced automotive industry, precision, efficiency, and reliability are essential for producing high-quality vehicles. Computer Numerical Control (CNC) machines have revolutionized manufacturing by offering unmatched accuracy and versatility. Let’s explore how CNC machines shape automotive production, their evolution, and their impact on the industry.
Evolution of CNC Machines
CNC machines mark a significant shift from traditional methods by automating manufacturing with computer-guided precision. They use software to control machinery, ensuring consistent quality and allowing for intricate designs that were once challenging to achieve manually.
Early CNC machines were basic, operating on limited axes for tasks like drilling and milling. Advancements have since enabled modern CNC machines to operate on multiple axes simultaneously, crucial for complex automotive parts requiring precise tolerances.
Key Applications in Automotive Manufacturing
Precision Machining: CNC machines excel in crafting exact components, such as engine parts and chassis, ensuring uniformity in size and finish critical for vehicle safety.
Prototyping and Customization: Automakers use CNC machines extensively for testing new designs and creating specialized parts quickly, reducing development times for new vehicle models.
Mass Production: Beyond precision, CNC machining supports high-volume production efficiently. Automated processes and optimized tool paths meet demand without compromising quality.
Complex Geometry: Automotive parts like turbocharger housings demand intricate shapes. CNC machines with multi-axis capabilities handle these complexities flawlessly, ensuring perfect fit and function.
Tooling and Molds: CNC machines create precise molds and tooling for automotive manufacturing processes like stamping and injection molding, guaranteeing consistent part quality.
Advantages of CNC Machines in Automotive Manufacturing
Accuracy and Consistency: Operating with micron-level precision, CNC machines minimize errors, reduce waste, and streamline production timelines.
Efficiency: Automated operations decrease manual labor, enhancing throughput and making CNC machining ideal for high-speed automotive production lines.
Flexibility: CNC machines swiftly adapt to various tasks and designs, crucial for responding to market demands and customizing vehicle features.
Cost-Effectiveness: Despite initial investments, CNC machines lower long-term costs through reduced labor, less scrap, and optimal resource use, ensuring profitability.
Quality Assurance: Equipped with advanced monitoring systems, CNC machines maintain consistent quality. Real-time analysis detects issues early, improving product reliability.
Future Trends and Innovations
The future of CNC machines in automotive manufacturing looks promising with:
Industry 4.0 Integration: CNC machines will integrate with IoT devices, enabling real-time data exchange and predictive maintenance, optimizing efficiency and minimizing downtime.
Additive Manufacturing: Hybrid CNC machines combining additive and subtractive capabilities will become standard, allowing for intricate designs and customized automotive components.
AI and Machine Learning: AI-driven algorithms will optimize CNC processes, predicting tool wear, refining cutting paths, and boosting overall efficiency based on historical data.
Sustainability Initiatives: CNC machines will support automotive sustainability goals through eco-friendly materials, optimized processes, and reduced waste, aligning with global environmental standards.
Conclusion
CNC machines have revolutionized automotive manufacturing, providing precision, efficiency, and adaptability unmatched by traditional methods. From prototyping to mass production, these machines play a pivotal role in creating safer, reliable, and technologically advanced vehicles. As CNC technology continues to evolve, embracing these advancements will be crucial for automakers to stay competitive in a rapidly changing global market.