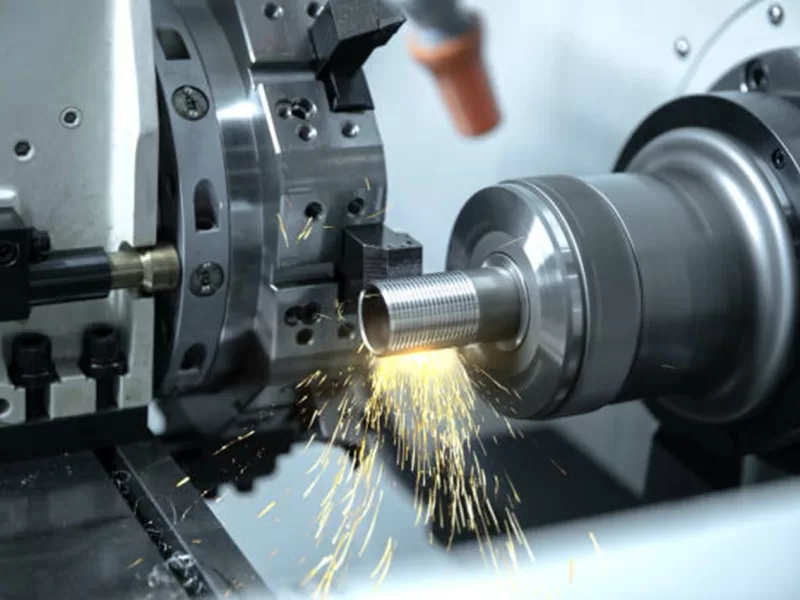
In the realm of modern manufacturing, CNC (Computer Numerical Control) machines reign supreme, providing unparalleled precision and efficiency in various industries. These sophisticated pieces of equipment are instrumental in producing intricate parts and components with utmost accuracy. However, like any mechanical system, CNC machines require regular maintenance to ensure optimal performance and longevity. In this blog, we’ll delve into essential maintenance tips for CNC machines, guiding you on how to prolong the life of your equipment and maximize its productivity.
Understanding the Importance of CNC Machine Maintenance
Maintenance isn’t just a routine task; it’s the lifeline that sustains the functionality and reliability of CNC machines. Picture these machines as finely tuned instruments, delicately orchestrating the dance of cutting tools with unparalleled precision. Like any instrument, they require regular tuning and care to perform at their best.
The importance of CNC machine maintenance becomes apparent when we consider the consequences of neglect. Without proper upkeep, these machines can quickly succumb to a myriad of issues. Accumulated debris, coolant contamination, and wear and tear on crucial components can spell disaster for precision and productivity.
- Imagine a CNC machine operating without regular cleaning. Dust, chips, and coolant residues accumulate, infiltrating delicate mechanisms and obstructing smooth operation. The result? Increased friction, decreased accuracy, and a higher likelihood of breakdowns. What was once a beacon of precision engineering now struggles to maintain tolerances, leading to costly rework and downtime.
- Lubrication is another cornerstone of CNC machine maintenance often overlooked. Just as our joints require oil to move smoothly, CNC machines rely on proper lubrication to minimize friction and prevent premature wear. Failure to lubricate adequately can result in increased power consumption, overheating, and accelerated deterioration of moving parts.
- Wear and tear are inevitable in any mechanical system, but vigilant inspection and timely replacement of worn components can mitigate their impact. Loose belts, worn bearings, and dulled cutting tools not only compromise performance but also pose safety risks to operators. Addressing these issues promptly is paramount to ensuring the longevity of CNC machines and the safety of personnel.
- Calibration is perhaps the most critical aspect of CNC machine maintenance when it comes to preserving precision. These machines operate with razor-thin tolerances, relying on precise alignments and settings to deliver accurate results. Regular calibration checks and adjustments are essential to counteract the effects of thermal expansion, tool wear, and other factors that can affect accuracy over time.
- In the digital age, software updates are another vital aspect of CNC machine maintenance. Manufacturers continually release updates and patches to improve performance, address bugs, and enhance security. Failure to keep the control software up to date not only hampers performance but also exposes the machine to potential cybersecurity threats.
CNC Machine Maintenance Tips: Ensuring Peak Performance
1. Regular Cleaning
Maintaining a clean working environment is crucial for CNC machines. Accumulated debris, chips, and coolant residues can impede the machine’s functionality and lead to premature wear of components. Regularly clean the machine’s surfaces, enclosures, and coolant tanks to prevent contamination and ensure smooth operation.
2. Lubrication
Proper lubrication is essential for reducing friction and preventing wear in moving parts. Follow manufacturer recommendations for lubrication intervals and use high-quality lubricants suitable for CNC applications. Check lubrication levels regularly and replenish as needed to keep the machine running smoothly.
3. Check for Wear and Tear
Inspect the machine for signs of wear, such as loose belts, damaged bearings, or worn-out cutting tools. Addressing these issues promptly can prevent further damage and maintain the machine’s accuracy and reliability. Replace worn components and tools according to the manufacturer’s specifications.
4. Calibration
Regular calibration is essential for ensuring the accuracy of CNC machines. Check and adjust parameters such as tool offsets, axis alignments, and spindle runout to maintain precision in machining operations. Perform calibration tasks as per the recommended schedule to uphold the machine’s performance standards.
5. Software Updates
Keep the CNC control software up to date with the latest versions and patches provided by the manufacturer. Software updates not only enhance performance but also address security vulnerabilities and improve compatibility with newer technologies. Regularly check for updates and implement them as necessary.
6. Coolant Management
If your CNC machine uses coolant for cutting operations, proper coolant management is crucial. Monitor coolant levels, cleanliness, and concentration to ensure optimal machining conditions. Clean or replace coolant filters regularly and dispose of used coolant in accordance with environmental regulations.
7. Electrical Components
Inspect electrical components such as cables, connectors, and circuit boards for signs of damage or wear. Loose connections or corroded components can compromise the machine’s functionality and pose safety hazards. Keep electrical systems well-maintained and address any issues promptly.
8. Safety Checks
Prioritize safety by verifying that all safety features, such as emergency stop buttons, interlocks, and guards, are functioning correctly. Conduct regular safety inspections and provide comprehensive training to machine operators on safe operating practices. Safety should always be a top priority in CNC machine maintenance.
9. Operator Training
Invest in thorough training for CNC machine operators to ensure they understand maintenance procedures and can identify potential issues. Well-trained operators can play a vital role in early detection of problems and contribute to the overall efficiency and reliability of the equipment.
10. Documentation
Maintain detailed records of maintenance activities, including inspection reports, repair logs, and service schedules. Documentation serves as a valuable reference for tracking the machine’s maintenance history and identifying patterns or recurring issues. It also facilitates compliance with regulatory requirements and aids in troubleshooting.
Mistakes Operators make while Maintaining CNC Machines
Maintaining CNC machines is a critical responsibility that operators must undertake to ensure optimal performance and longevity of these sophisticated pieces of equipment. However, despite their best intentions, operators can sometimes make mistakes that inadvertently compromise the effectiveness of maintenance efforts. Let’s delve into some common mistakes operators may make while maintaining CNC machines:
Inadequate Cleaning: One of the most prevalent mistakes is insufficient cleaning of CNC machines. Operators may overlook the importance of thorough cleaning, leading to the accumulation of chips, debris, and coolant residues. This oversight can impede the smooth operation of the machine and contribute to premature wear of components.
Neglecting Lubrication: Proper lubrication is essential for reducing friction and preventing wear in moving parts. However, operators may overlook lubrication intervals or use the wrong type of lubricant. This mistake can result in increased friction, overheating, and accelerated deterioration of critical components.
Ignoring Wear and Tear: Operators may fail to identify and address signs of wear and tear on CNC machines. Loose belts, worn bearings, and dulled cutting tools can compromise performance and accuracy. Ignoring these issues can lead to costly repairs and downtime in the long run.
Skipping Calibration Checks: Regular calibration is crucial for maintaining the accuracy of CNC machines. However, operators may overlook or delay calibration checks, assuming that the machine is operating within acceptable tolerances. This oversight can result in inaccuracies in machining operations, affecting the quality of the finished products.
Overlooking Software Updates: CNC control software requires regular updates to improve performance, address bugs, and enhance security. Operators may neglect to install these updates, believing that the current software version is sufficient. However, outdated software can hinder the machine’s functionality and expose it to potential cybersecurity risks.
Improper Coolant Management: If the CNC machine uses coolant for cutting operations, operators may mishandle coolant management. Failure to monitor coolant levels, cleanliness, and concentration can lead to poor machining conditions and affect the quality of machined parts.
Lack of Electrical Component Inspection: Electrical components play a crucial role in CNC machine operation. However, operators may overlook regular inspection of cables, connectors, and circuit boards for signs of damage or wear. Neglecting electrical component maintenance can result in malfunctions or safety hazards.
Disregarding Safety Protocols: Operators may overlook safety protocols while performing maintenance tasks on CNC machines. This includes failing to follow lockout/tagout procedures, bypassing safety interlocks, or neglecting to wear personal protective equipment. Such oversights can lead to accidents or injuries in the workplace.
Insufficient Operator Training: Inadequate training can lead to mistakes in CNC machine maintenance. Operators may lack the necessary knowledge and skills to perform maintenance tasks effectively or identify potential issues. Investing in comprehensive operator training is essential for ensuring proper maintenance practices.
Failure to Document Maintenance Activities: Proper documentation of maintenance activities is crucial for tracking the machine’s maintenance history and identifying recurring issues. Operators may overlook the importance of maintaining detailed records, making it challenging to assess the effectiveness of maintenance efforts over time.
Conclusion
In conclusion, proactive maintenance is essential for prolonging the life of CNC machines and optimizing their performance. By following these maintenance tips diligently, manufacturers can minimize downtime, reduce repair costs, and maximize the return on investment in CNC technology. Remember, a well-maintained CNC machine is not just a piece of equipment—it’s a cornerstone of efficient and reliable manufacturing operations.