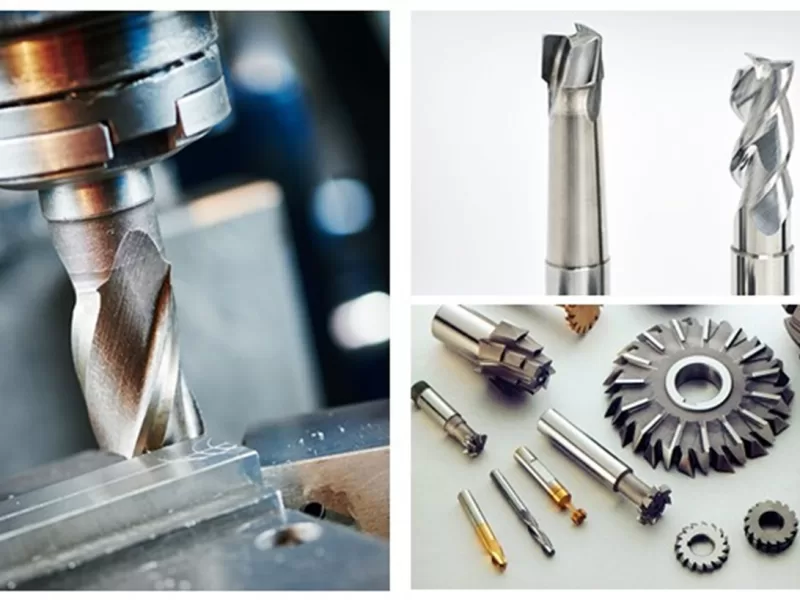
In the realm of modern manufacturing, CNC machines stand as the backbone of precision and efficiency. These computer-controlled marvels churn out intricate components with unparalleled accuracy, transforming raw materials into finished products across various industries. However, the true magic of CNC machining lies not just in the machines themselves, but also in the tools they wield. Selecting the right cutting tools for CNC machines is paramount to unlocking their full potential. In this detailed guide, we delve into the intricacies of tool selection, empowering you to make informed choices that optimize your machining processes.
Understanding CNC Machines and Cutting Tools
Before diving into the nuances of tool selection, let’s grasp the fundamentals of CNC machining and cutting tools. CNC machines encompass a diverse array of equipment, including milling machines, lathes, routers, and plasma cutters, each tailored to specific machining tasks. These machines rely on cutting tools to shape materials into desired forms, be it intricate components for aerospace applications or finely crafted furniture pieces.
Automated Manufacturing Tools: CNC machines, short for Computer Numerical Control machines, are advanced manufacturing tools that automate various machining processes. They are widely used across industries for their ability to precisely shape raw materials into finished products.
Types of CNC Machines: CNC machines come in various types, each suited to specific machining tasks. These types include milling machines, lathes, routers, and plasma cutters. Each type has its own set of capabilities and applications, ranging from milling intricate components to turning cylindrical parts.
Controlled by Computer Programs: Unlike conventional manual machines, CNC machines are controlled by computer programs. These programs, often generated using CAD (Computer-Aided Design) software and converted into machine-readable code (typically G-code) through CAM (Computer-Aided Manufacturing) software, dictate the movements of the cutting tools with high precision.
Key Factors in Tool Selection
Machining Operations: Identify the specific machining operations your project requires, such as milling, turning, drilling, or engraving. Different operations demand specialized tools optimized for their respective tasks.
Tool Materials: Consider the material composition of the cutting tools, as it profoundly influences performance and durability. Common tool materials include high-speed steel (HSS), carbide, and ceramic, each offering unique advantages in terms of hardness, toughness, and heat resistance.
Tool Coatings: Explore the realm of tool coatings, which enhance tool life and performance by reducing friction, dissipating heat, and preventing chip adhesion. Popular coatings include titanium nitride (TiN), titanium carbonitride (TiCN), and diamond-like carbon (DLC).
Cutting Parameters: Fine-tune cutting parameters such as speed, feed rate, and depth of cut to optimize tool performance and achieve desired outcomes. Balancing these parameters ensures efficient material removal while preserving tool integrity.
Tool Geometry: Pay attention to tool geometry, encompassing factors like flute design, helix angle, and edge geometry. Optimal tool geometry facilitates chip evacuation, minimizes cutting forces, and enhances surface finish.
Maximizing Tool Performance
Once armed with insights into tool selection, the journey doesn’t end there. Maximizing tool performance entails meticulous attention to detail throughout the machining process. Regular tool maintenance, proper tool handling, and adherence to recommended cutting parameters are essential for extending tool life and ensuring consistent results.
Regular Maintenance: Proper maintenance of cutting tools, including sharpening, cleaning, and inspection, is essential for prolonging tool life and ensuring consistent machining performance. Regular maintenance prevents tool wear and breakage, thereby reducing downtime and enhancing productivity.
Optimal Handling: Correct handling practices, such as proper storage and handling techniques, prevent damage to cutting tools and extend their longevity. Mishandling tools can lead to premature wear, breakage, and compromised machining performance.
Adherence to Parameters: Adhering to recommended cutting parameters, such as cutting speed, feed rate, and depth of cut, is critical for maximizing tool performance and achieving desired machining outcomes. Deviating from recommended parameters can result in tool wear, poor surface finish, and decreased productivity.
The Importance of Cost-Effectiveness
While investing in premium cutting tools yields undeniable benefits in terms of performance and longevity, cost-effectiveness remains a crucial consideration. Striking a balance between tool quality and affordability is key to optimizing manufacturing operations without breaking the bank.
Balancing Quality and Affordability: While investing in high-quality cutting tools offers long-term benefits in terms of performance and durability, it’s essential to balance quality with affordability. Evaluating the cost-effectiveness of cutting tools involves considering factors such as initial cost, tool life, maintenance requirements, and overall machining efficiency.
Total Cost of Ownership: Assessing the total cost of tool ownership, which includes initial purchase cost, maintenance expenses, and replacement costs, provides a comprehensive understanding of the long-term economic viability of cutting tools. By considering the total cost of ownership, manufacturers can make informed decisions that optimize cost-effectiveness while maintaining machining quality and productivity.
Conclusion
Choosing cutting tools for CNC machines is a multifaceted endeavor that demands careful consideration of various factors, from machining operations and tool materials to cutting parameters and cost-effectiveness. By leveraging the insights provided in this detailed guide, you can navigate the labyrinth of tool selection with confidence, unlocking the full potential of CNC machining and propelling your projects to new heights of precision and efficiency.