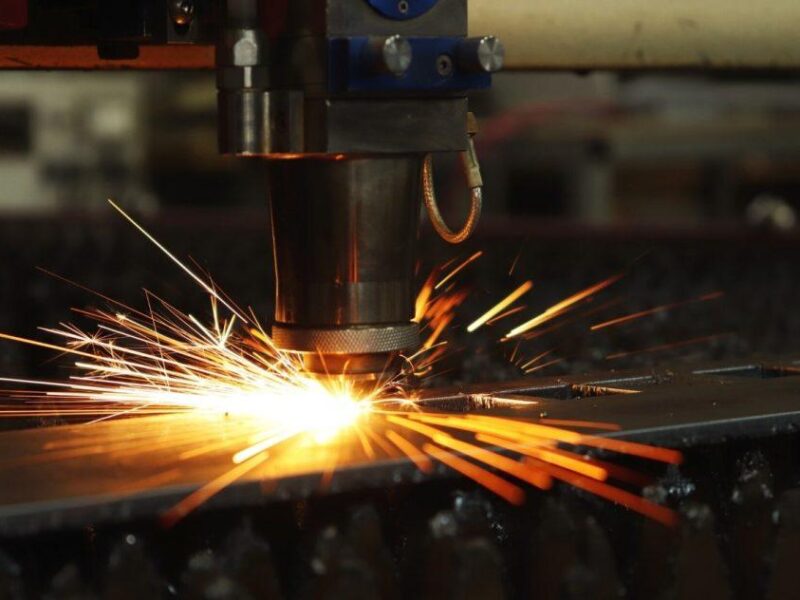
Introduction
In the world of CNC machining, achieving optimal cost-efficiency is a pivotal goal for businesses aiming to thrive in competitive markets. A substantial aspect of this efficiency lies in the judicious use of materials and tools, allowing for both cost savings and enhanced productivity. This article explores effective strategies and approaches to streamline CNC machining processes, emphasizing the economical utilization of materials and tools.
In the dynamic landscape of manufacturing, precision and efficiency are fundamental pillars driving success in CNC machining. At the core of this intricate process lie the judicious utilization of materials and tools, pivotal elements that not only impact costs but also shape the quality and competitiveness of the final product.
In our exploration of cost-saving strategies within CNC machining, we delve into the art of optimizing material and tool efficiency. From the careful selection of materials to the strategic maintenance of cutting-edge tools, this article aims to unravel the key tactics and approaches that empower businesses to curtail expenses without compromising on quality or productivity.
By understanding the significance of material choice, embracing innovative design techniques, and fine-tuning machining processes, manufacturers can unlock substantial savings while elevating their output. This comprehensive guide delves into actionable insights and strategies, offering a roadmap to harness the full potential of CNC machining operations.
Understanding the Significance of Material and Tool Efficiency
In CNC machining, materials and tools represent the cornerstone of production. Optimizing their usage not only impacts operational costs but also influences the overall quality of manufactured components. Wastage of materials or premature tool wear can substantially escalate expenses and diminish profitability. Hence, implementing strategies to maximize material and tool efficiency becomes imperative.
Selecting the Right Materials
Choosing appropriate materials is the initial step toward cost-effective CNC machining. Opt for materials that match the required specifications while considering factors such as durability, availability, and cost-effectiveness. Utilizing standardized materials can also streamline procurement processes, potentially reducing expenses.
Efficient Material Management
Effective material management involves minimizing waste and maximizing utilization. Implementing techniques like nesting and optimizing part orientation within the raw material sheet can significantly reduce scrap material. Additionally, recycling or repurposing leftover materials can further curtail costs and environmental impact.
Strategic Tool Selection and Maintenance
Tools are indispensable assets in CNC machining. Employing high-quality tools suited to specific machining tasks ensures optimal performance and longevity. Regular maintenance, including timely sharpening or replacement, prevents premature tool wear, reducing the frequency of tool purchases and enhancing operational efficiency.
Precision Programming
When we talk about precision programming in CNC machining, it’s like choreographing a dance for the machines. It’s about creating the perfect set of instructions to guide those tools across the material in the most efficient and precise way possible.
Smart Tool Movements: Imagine planning the most efficient route on a map. Engineers and programmers do something similar with cutting tools, figuring out the best path to minimize waste and maximize accuracy.
Software Magic: We’ve got these nifty tools called CAM software. They let us visualize the whole machining process before it even happens. It’s like a simulator for cutting stuff, helping us fine-tune speeds, feeds, and tool engagements for the best outcome.
Faster, Better, Smarter: Precision programming isn’t just about speed; it’s about efficiency. We’re all about reducing the time it takes to make something while making sure it’s top-notch quality.
Inventory Management
Think of inventory management as a balancing act. It’s about having just the right amount of materials and products without drowning in excess or running out at the wrong time.
Just-in-Time Magic: This is like the magician’s trick of getting things right when needed. Instead of stockpiling materials, we get them in just as we need them. Saves space and money!
Planning Like a Pro: Ever heard of material requirement planning? It’s like having a crystal ball for predicting what materials we’ll need and when. This keeps the production line smooth without any “Oops, we’re out of this!” moments.
Friends in the Supply Chain: Having great relationships with suppliers is like having reliable friends. They make sure our materials show up on time and sometimes even give us good deals. It’s a win-win!
Continuous Monitoring and Analysis
Think of this as our CNC machinist’s superpower—the ability to always keep an eye on how things are going and fixing stuff before it becomes a problem.
Real-time Spy Work: We’ve got sensors and monitors that give us instant updates on how the machines are doing. If something’s not right, we know it pronto and fix it before it goes wonky.
Numbers Tell Tales: Analyzing all the data we collect helps us spot trends and figure out where things could be smoother. It’s like detective work but for machines!
Always Getting Better: By keeping an eagle eye on the processes, we’re constantly fine-tuning things. It’s all about finding ways to save time, materials, and money while making sure our products are top-notch.
Cost-Saving Strategies in CNC Machining
In the realm of CNC machining, efficiency isn’t just a goal; it’s the lifeline that defines success. Delving into the world where precision meets innovation, this exploration focuses on the crux of profitability: cost-saving strategies. The art of optimizing resources—materials and tools—takes centre stage, revealing the secrets that drive savings without compromising quality.
From shrewd material selection to fine-tuning tool utilization, this guide unravels the blueprint for businesses seeking to trim expenses while elevating their CNC machining prowess. Join us in uncovering the key strategies that not only slash costs but also sharpen the competitive edge in the dynamic landscape of manufacturing.
1. Design Optimization for Material Efficiency
Collaboration between designers and machinists to optimize part designs can lead to substantial material savings. Employing design software that facilitates efficient nesting or considering alternative geometries without compromising functionality aids in reducing material wastage.
2. Precision Programming and Toolpath Optimization
Fine-tuning machining programs and toolpaths enhances efficiency by reducing cycle times and minimizing unnecessary tool movements. Advanced CAM software allows for intricate control over machining processes, optimizing tool engagement and minimizing tool wear.
3. Inventory Management and Lean Practices
Maintaining an optimal inventory level through just-in-time practices reduces holding costs and minimizes the risk of material obsolescence. Adopting lean manufacturing principles eliminates non-value-added activities, streamlining operations and reducing overheads.
4. Continuous Monitoring and Analysis
Regular monitoring of machining processes allows for the identification of inefficiencies or potential areas for improvement. Data-driven analysis enables informed decision-making, facilitating adjustments to enhance material and tool efficiency continually.
Saving Money While Crafting Excellence
Picture this: crafting precision parts with finesse while keeping a watchful eye on your bottom line. That’s the beauty of cost-saving strategies in CNC machining—the art of making every cut count without compromising on quality.
Material Matters
Choosing the right materials is like picking the perfect ingredients for a recipe. It’s about finding the balance between quality, cost, and availability. Opting for standardized materials not only simplifies the buying process but also keeps the expenses in check.
Smart Design, Less Waste
Imagine designing a puzzle where every piece fits snugly without excess. That’s what efficient design does in CNC machining. Smart design software helps us arrange parts to minimize material waste. It’s like a Tetris game but for crafting components.
Tools That Go the Extra Mile
Tools are our trusty sidekicks in the CNC world. Choosing top-notch tools designed for specific tasks ensures they last longer and perform better. Regular maintenance keeps them sharp and ready, saving us from premature replacements.
Cutting Waste, Not Corners
Cutting isn’t just about shaping materials; it’s about cutting costs sensibly. Optimizing toolpaths and fine-tuning programming reduces unnecessary movements, slashes cycle times, and minimizes material waste. It’s like finding the shortest route on a road trip, but with machines.
Lean Inventory, Smart Moves
Having the right materials at the right time is like having a secret stash in your pocket. Adopting just-in-time practices ensures we’re not drowning in inventory costs or left high and dry when we need materials urgently.
Watch, Learn, Improve
We’re like detectives, constantly analyzing our processes. Real-time monitoring gives us the inside scoop on machine performance. By crunching the numbers, we identify bottlenecks and make tweaks for smoother operations.
Cost-saving in CNC machining isn’t just about cutting expenses; it’s about crafting excellence while being smart about every move. It’s the symphony of precision, design, tools, and savvy practices that ensure we deliver quality while saving every penny possible.
Conclusion
Efficient utilization of materials and tools stands as a cornerstone for cost-effective CNC machining. By adopting a proactive approach encompassing material selection, smart design, precise programming, and strategic inventory management, businesses can significantly reduce operational costs while concurrently enhancing productivity and product quality. Embracing these strategies empowers CNC machining enterprises to navigate competitive landscapes while maintaining a strong foothold in the market.