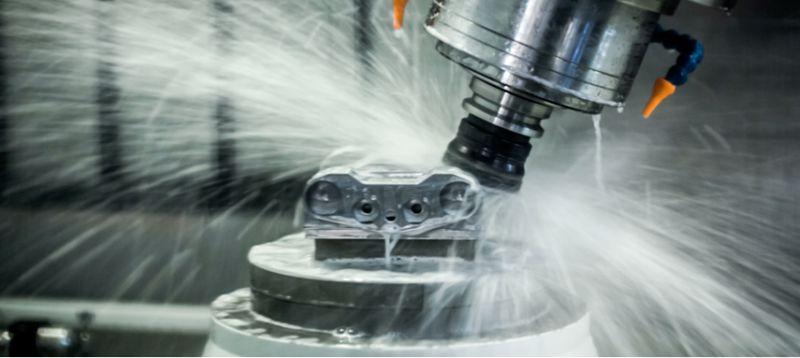
Introduction
In the realm of modern manufacturing, CNC machining stands as a pillar of precision and efficiency. Its applications extend far beyond conventional manufacturing, permeating industries such as automotive, aerospace, and a diverse array of others. Let’s delve into the multifaceted landscape of CNC machining, exploring its pivotal role and diverse applications across different sectors.
CNC Machining in the Automotive Industry
In the intricate world of automotive manufacturing, precision and efficiency reign supreme. From crafting engine components to shaping intricate body parts, the utilization of cutting-edge technology has redefined the industry. One of the pivotal advancements that have transformed automotive production is Computer Numerical Control (CNC) machining.
Precision Redefined
CNC machining has become the cornerstone of modern automotive manufacturing due to its unparalleled precision and versatility. This technology involves computer-controlled machines that precisely carve out components from raw materials such as metal, plastic, or composite substances. These machines interpret digital designs, translating them into precise movements to shape and refine automotive parts with meticulous accuracy.
Enhanced Efficiency
The automotive industry’s demand for consistency and accuracy finds an optimal match in CNC machining. Unlike traditional manufacturing methods, CNC processes significantly reduce human error, ensuring a consistently high standard of production. The ability to automate processes not only enhances precision but also expedites production timelines, facilitating quicker turnaround times without compromising quality.
Diverse Applications
The applications of CNC machining within the automotive industry are vast and multifaceted. From creating engine components like cylinder heads, pistons, and crankshafts to intricate parts like gears, shafts, and brackets, CNC technology offers a solution for manufacturing these components with exceptional precision and efficiency.
Moreover, CNC machining plays a crucial role in crafting complex body parts, ensuring seamless designs and impeccable finishing. The ability to replicate intricate designs consistently has led to the production of sleeker, aerodynamically superior automotive exteriors.
Adapting to Innovation
As automotive designs evolve and technological innovations surge forward, CNC machining continues to adapt and evolve. Integration with advanced software and the utilization of multi-axis machining centers have further expanded the capabilities of CNC technology. This evolution enables the creation of more complex, lightweight, and durable automotive components that meet the demands of modern vehicles.
Sustainability and CNC Machining
Beyond precision and efficiency, CNC machining also contributes to sustainability in automotive manufacturing. By optimizing material usage and minimizing waste through precise cutting and shaping, CNC technology aligns with the industry’s drive towards eco-conscious practices, reducing the environmental impact of automotive production processes.
CNC machining stands as a testament to the fusion of technology and automotive manufacturing. Its precision, efficiency, and adaptability have revolutionized the industry, allowing for the creation of vehicles that not only meet but exceed the demands of modern consumers. As advancements continue to push the boundaries of innovation, CNC machining remains an indispensable tool shaping the future of automotive engineering.
CNC Machining in Aerospace
In the realm of aerospace manufacturing, precision, reliability, and uncompromising quality are paramount. At the heart of producing the intricate components that power modern aviation lies Computer Numerical Control (CNC) machining—a technology that has revolutionized the aerospace industry.
Precision Engineering
CNC machining stands as the cornerstone of aerospace manufacturing, offering an unparalleled level of precision and accuracy. This technology employs computer-guided machines to sculpt and refine complex components from raw materials, ranging from metals to advanced alloys and composites. These machines meticulously interpret digital designs, executing intricate movements to craft aerospace parts with micron-level precision.
Unmatched Quality Assurance
In an industry where safety and performance are non-negotiable, CNC machining emerges as a key enabler of quality assurance. By significantly reducing human error and ensuring consistent production standards, CNC processes guarantee the creation of aerospace components that adhere to the strictest quality benchmarks. This level of reliability is crucial for the structural integrity and functionality of aerospace systems.
Diverse Applications in Aerospace
The applications of CNC machining in aerospace are diverse and far-reaching. From crafting critical engine components like turbine blades, housings, and casings to intricate parts such as brackets, actuators, and fasteners, CNC technology offers an indispensable solution for manufacturing components that meet the rigorous demands of aerospace engineering.
Moreover, CNC machining plays a pivotal role in producing lightweight and aerodynamically superior parts crucial for aircraft performance. The ability to create complex geometries with precision ensures that aerospace systems achieve optimal efficiency and durability while maintaining stringent weight constraints.
Advanced Innovation and CNC Technology
The aerospace industry continually pushes the boundaries of technological innovation, and CNC machining evolves in tandem. Integration with cutting-edge software, utilization of multi-axis machining, and the incorporation of additive manufacturing techniques have further expanded the capabilities of CNC technology. This evolution enables the creation of components that are not only highly complex but also lighter, stronger, and more resistant to extreme conditions—a necessity in aerospace engineering.
Sustainability and CNC Machining in Aerospace
Beyond precision and performance, CNC machining contributes to sustainability in aerospace manufacturing. By optimizing material usage and minimizing waste through precise machining, CNC technology aligns with the industry’s efforts toward eco-friendly practices, reducing the environmental footprint of aerospace production processes.
CNC machining stands as a testament to the fusion of innovation and aerospace manufacturing. Its precision, reliability, and adaptability have propelled the industry forward, enabling the creation of aircraft that exemplify cutting-edge engineering. As aerospace technology continues to advance, CNC machining remains an indispensable tool in shaping the future of aerospace exploration and transportation.
Expanding Beyond: CNC Machining in Other Industries
Beyond automotive and aerospace, CNC machining leaves its mark in numerous other sectors. From medical device manufacturing to electronics and even in the production of consumer goods, CNC technology’s versatility shines.
The advent of Computer Numerical Control (CNC) machining has revolutionized manufacturing across numerous industries beyond aerospace and automotive sectors. Its precision, efficiency, and adaptability have positioned CNC technology as an indispensable tool across a multitude of diverse fields, shaping the way products are crafted and innovations are brought to life.
Electronics Industry
In the realm of electronics manufacturing, the demand for intricately designed components with tight tolerances has made CNC machining indispensable. From circuit boards to intricate casings for electronic devices, CNC technology ensures precise production of components critical for the functioning of modern electronic gadgets.
Medical Sector
Precision and accuracy are paramount in the medical field, and CNC machining plays a pivotal role in crafting medical devices, implants, and prosthetics. From intricate surgical tools to patient-specific implants, CNC technology enables the production of high-quality, customized medical equipment that meets stringent safety and reliability standards.
Tooling and Die Making
CNC machining is the backbone of tool and die making industries, where precision is non-negotiable. It allows for the creation of molds, dies, and tooling with intricate geometries, facilitating the mass production of consumer goods, ensuring uniformity and consistency in their manufacturing processes.
Architectural and Design
In architecture and design, CNC machining enables the creation of intricate and customized components, from decorative elements to complex structural parts. It revolutionizes the fabrication of architectural details, furniture, and sculptures, allowing designers to bring intricate concepts to life with precision and efficiency.
Renewable Energy
The renewable energy sector benefits from CNC machining in the production of components for wind turbines, solar panels, and energy storage systems. CNC technology ensures the creation of precise parts critical for harnessing renewable energy efficiently, contributing to sustainable energy solutions.
Customized Manufacturing and Prototyping
CNC machining has facilitated the rise of customized manufacturing and rapid prototyping across various industries. Its ability to quickly produce complex prototypes and customized parts allows for faster product development cycles and the testing of innovative ideas before full-scale production.
The impact of CNC machining transcends specific industries, permeating into diverse sectors and playing a pivotal role in shaping modern manufacturing and innovation. Its precision, versatility, and adaptability continue to drive advancements, enabling industries to push the boundaries of what is possible, leading to a future defined by precision, efficiency, and unparalleled quality across various sectors.
Innovations and Advancements in CNC Technology
The evolution of Computer Numerical Control (CNC) technology has been a testament to human ingenuity and technological progress. From its inception as a means of automating machining processes to its current state as a pinnacle of precision engineering, CNC has continually pushed the boundaries of what is achievable in manufacturing.
Integration of Advanced Software
One of the foremost advancements in CNC technology is the integration of sophisticated software solutions. Modern CNC systems leverage advanced CAD (Computer-Aided Design) and CAM (Computer-Aided Manufacturing) software, enabling seamless translation of digital designs into precise machining instructions. This integration allows for complex geometries, intricate patterns, and highly detailed specifications to be realized with unprecedented accuracy.
Multi-Axis Machining
The introduction of multi-axis machining capabilities has revolutionized CNC operations. Beyond traditional three-axis systems, machines equipped with five or more axes offer enhanced versatility, allowing for intricate and compound machining operations. This advancement enables the production of complex components with streamlined processes, reducing the need for multiple setups and minimizing production time.
High-Speed Machining
The advent of high-speed machining has significantly increased production efficiency. CNC machines now boast faster spindle speeds and improved tooling capabilities, enabling rapid material removal rates without compromising accuracy. This innovation facilitates shorter production cycles, making CNC machining more time-efficient while maintaining the highest standards of precision.
Additive Manufacturing Integration
The convergence of CNC machining with additive manufacturing techniques marks a groundbreaking development. Hybrid CNC machines now combine subtractive and additive manufacturing processes in a single system, allowing for intricate designs to be built layer by layer and then precisely machined to perfection. This integration expands the possibilities for creating highly complex and customized parts with unparalleled precision.
Automation and Industry 4.0 Integration
CNC technology has embraced the principles of Industry 4.0 by integrating automation and data exchange. Smart CNC systems equipped with sensors and IoT (Internet of Things) capabilities enable real-time monitoring, predictive maintenance, and adaptive machining processes. This integration enhances productivity, minimizes downtime, and optimizes resource utilization, paving the way for more efficient and cost-effective manufacturing.
Materials and Sustainability
Advancements in CNC technology have also expanded the range of machinable materials. CNC machines now handle a diverse array of materials, including advanced alloys, composites, and exotic metals. Additionally, CNC machining has evolved to optimize material usage, reduce waste, and support sustainable manufacturing practices, aligning with global efforts toward environmental conservation.
The continuous innovations and advancements in CNC technology have redefined the landscape of manufacturing. From enhanced precision and speed to integration with cutting-edge techniques, CNC technology continues to propel industries forward, enabling the creation of complex, high-quality components that drive innovation across various sectors.
Conclusion
CNC machining isn’t confined to a singular industry; it’s a driving force across diverse sectors, ensuring precision, reliability, and innovation. Its contributions to automotive, aerospace, and a myriad of other industries underscore its indispensable role in shaping modern manufacturing. As technology advances, CNC machining will continue to be the cornerstone of progress, fostering innovation and propelling industries forward.