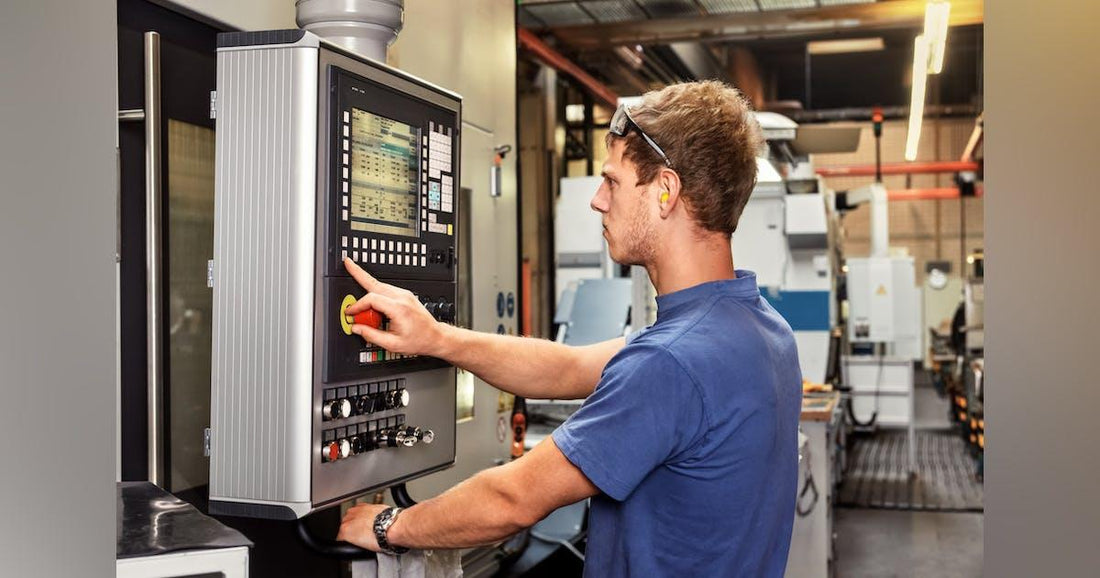
Troubleshooting Common CNC Machine Problems: Practical tips and solutions
Introduction
CNC (Computer Numerical Control) machines have revolutionized manufacturing processes, offering precision and automation. However, their complexity means encountering issues is almost inevitable. Knowing how to troubleshoot these problems is crucial to maintain productivity and reduce downtime.
Precision, automation, and efficiency—these are the hallmarks of CNC (Computer Numerical Control) machines that have transformed the landscape of modern manufacturing. From intricate designs to large-scale production, these marvels of technology have redefined what’s possible. However, alongside their incredible capabilities comes the undeniable truth: the complexity of CNC machines often leads to technical hitches and operational glitches.
Imagine a scenario: a smoothly running production line suddenly halts, the fault light on the CNC machine blinking incessantly. In that critical moment, understanding the intricacies of troubleshooting becomes paramount. It’s in these instances that practical knowledge about the common problems haunting CNC machines becomes a lifeline.
In this comprehensive guide, we delve into the world of troubleshooting—unveiling the prevalent issues that plague CNC machines, offering practical tips and ingenious solutions. From mechanical woes causing misalignment to enigmatic software errors disrupting the precision of operations, each aspect is dissected, decoded, and empowered with actionable advice.
Common CNC Machine Problems
CNC machines are the backbone of precision manufacturing, but even these technological marvels aren’t immune to glitches. Understanding the most frequent issues encountered with these machines is pivotal for ensuring smooth operations.
Mechanical Issues: These machines are intricate assemblies of mechanical components, and wear and tear are inevitable over time. Misalignments, backlash, or inadequate lubrication often plague CNC machines, impacting their accuracy and functionality. Misalignments, for instance, occur due to various factors such as improper setup or gradual shifts in the machine’s components. This can lead to skewed cuts or inaccurate dimensions in the final product. Backlash, on the other hand, results in a lost motion due to clearance between mechanical components, leading to imprecise tool movements. Regular maintenance, including checks for wear and tear, proper lubrication, and timely alignments, can significantly mitigate these issues.
Electrical Problems: The electrical system in CNC machines is intricate, comprising numerous wiring connections, power supplies, servos, and feedback mechanisms. Problems in this domain, such as faulty wiring, power fluctuations, or malfunctions in servos or feedback systems, can disrupt the machine’s performance. Even a slight glitch in the electrical system can result in erratic movements or complete machine failure. Adequate grounding, routine checks for loose connections, and ensuring stable power sources are crucial to prevent and address such electrical issues.
Software and Programming Troubles: CNC machines operate on intricate software and programming languages like G-code. Issues in programming or software compatibility often lead to errors in machining. A misplaced command in the code or an incompatible software update can cause the machine to operate inaccurately or stop mid-process. Understanding the nuances of the programming language and regularly updating and testing software are crucial to avoid such problems.
Each of these issues can significantly impact production efficiency and output quality. Timely identification and resolution are key to minimizing downtime and maintaining optimal machine performance.
Practical Tips for Troubleshooting
Effectively troubleshooting CNC machine problems requires a combination of technical expertise, a proactive approach to maintenance, utilization of diagnostic tools, and a culture that promotes continuous learning and problem-solving. By implementing these practical tips and strategies, organizations can streamline troubleshooting processes, minimize downtime, and optimize the performance of their CNC machines.
Regular Maintenance: Establishing a comprehensive maintenance schedule is the cornerstone of troubleshooting CNC machine problems. Regular checks for wear and tear, proper lubrication, and alignments can prevent many mechanical issues. Incorporate a maintenance log to track and schedule routine inspections, ensuring no critical maintenance tasks are overlooked.
Diagnostic Tools and Techniques: Equipping your team with the right diagnostic tools is crucial for efficient troubleshooting. Tools like multimeters, dial indicators, oscilloscopes, and alignment gauges aid in identifying mechanical and electrical issues accurately. Train operators and technicians on how to use these tools effectively to diagnose and resolve problems promptly.
Understanding Error Codes and Indicators: The error codes displayed by CNC machines often provide valuable insights into underlying issues. Create a comprehensive guide or manual that explains these codes, detailing the probable causes and recommended actions for each code. This resource can be invaluable in swiftly addressing problems as they arise.
Employee Training and Knowledge Sharing: A well-trained team is a key asset in troubleshooting CNC machine problems. Invest in comprehensive training programs for operators, technicians, and programmers to enhance their understanding of the machine’s intricacies. Encourage a culture of knowledge sharing within the team, where experiences and insights are openly discussed and used to refine troubleshooting strategies.
Create Troubleshooting Protocols: Develop standardized protocols for troubleshooting common issues. Outline step-by-step procedures for identifying, diagnosing, and resolving typical problems encountered in CNC machines. Having these protocols readily available ensures consistency in troubleshooting approaches and minimizes errors due to oversight.
Document and Analyze Previous Issues: Maintain a detailed record of past issues and their resolutions. Analyze patterns in recurring problems to identify underlying causes or systemic issues. This historical data can provide valuable insights into preventive measures and help in predicting and preventing future problems.
Collaborate with Manufacturers and Experts: Establish relationships with CNC machine manufacturers or industry experts. Their insights and guidance can be invaluable in troubleshooting complex issues. Leverage their expertise for training, advice on best practices, and guidance on resolving intricate problems.
Encourage a Problem-Solving Culture: Foster an environment where problem-solving is encouraged and rewarded. Encourage employees to proactively report even minor issues and incentivize innovative solutions. This culture can lead to early detection and resolution of problems, preventing them from escalating into major disruptions.
Solutions for CNC Machining Problems
Unlocking the full potential of CNC (Computer Numerical Control) machines has revolutionized manufacturing, driving precision, efficiency, and innovation. Yet, amidst their prowess, these machines aren’t immune to challenges. When the fault light blinks or production halts, understanding the solutions to common CNC machining problems becomes paramount.
Welcome to our comprehensive guide on unraveling the intricacies of CNC machine troubleshooting. Today, we delve into a world where mechanical intricacies meet electrical complexities and where software precision encounters programming dilemmas. Each challenge holds within it a solution, a key to keeping these marvels of modern manufacturing at their pinnacle performance.
In this journey through the labyrinth of issues encountered in CNC machining, we equip you with actionable solutions. From addressing mechanical misalignments and electrical malfunctions to unraveling perplexing software glitches, our guide offers insights, tips, and strategies to combat these hurdles.
Mechanical Issues: Addressing mechanical problems requires a proactive approach. Regular maintenance, including scheduled inspections and part replacements, is vital. Misalignments can often be resolved by recalibrating the machine using precision tools like dial indicators. Backlash issues may necessitate adjustments in mechanical components to minimize clearance and improve precision. Implementing a robust preventive maintenance plan, including proper lubrication and timely replacements, can significantly extend the lifespan of mechanical parts and reduce the frequency of these issues.
Electrical Problems: Ensuring a stable electrical environment is crucial. Routine checks for loose connections, damaged wires, or power supply irregularities are essential preventive measures. Invest in surge protectors or stabilizers to safeguard against voltage fluctuations. Regularly testing the functionality of servos, encoders, and other electrical components can help identify and rectify issues early. Proper grounding and adherence to electrical safety standards are imperative to minimize electrical malfunctions.
Software and Programming Troubles: Addressing software-related issues involves a combination of technical expertise and systematic procedures. Regularly updating and validating software versions and ensuring compatibility with the CNC machine can prevent many problems. Verifying G-code programs thoroughly before execution and debugging them with simulation tools minimizes the risk of errors during operation. Investing in comprehensive training for operators and programmers to understand the intricacies of the software can significantly reduce the occurrence of programming-related issues.
Integrated Solutions: Often, a holistic approach combining preventive maintenance, employee training, and advanced diagnostic tools yields the most effective results. Implement predictive maintenance practices that use sensor data and analytics to anticipate potential issues before they escalate. Encourage a culture of continuous improvement, where feedback from operators and technicians is integrated into refining maintenance procedures and optimizing machine performance.
Troubleshooting CNC machine problems is a multifaceted task that requires a combination of technical expertise, proactive maintenance, and a commitment to continuous improvement. By addressing mechanical, electrical, and software-related issues through systematic solutions and preventive measures, manufacturers can minimize downtime, enhance machine reliability, and ultimately improve overall production efficiency.
Conclusion
Troubleshooting CNC machine problems is an integral part of maintaining efficient manufacturing processes. By understanding common issues, investing in maintenance, empowering employees with training, and implementing preventive measures, companies can significantly reduce downtime and enhance productivity.
In the realm of manufacturing, troubleshooting CNC machine problems isn’t just a task—it’s a mastery. From addressing mechanical intricacies to resolving software dilemmas, this journey through common issues has illuminated the path to seamless operations. By embracing practical tips, diagnostics, and a proactive approach to maintenance, we fortify the backbone of production.
Let this guide serve as a compass, navigating the complexities of CNC machines. As we conclude, remember: each challenge conquered, each solution applied, fuels the efficiency of these marvels. With these strategies in hand, let’s empower the industry to forge ahead, keeping CNC machines at their zenith of precision and productivity.