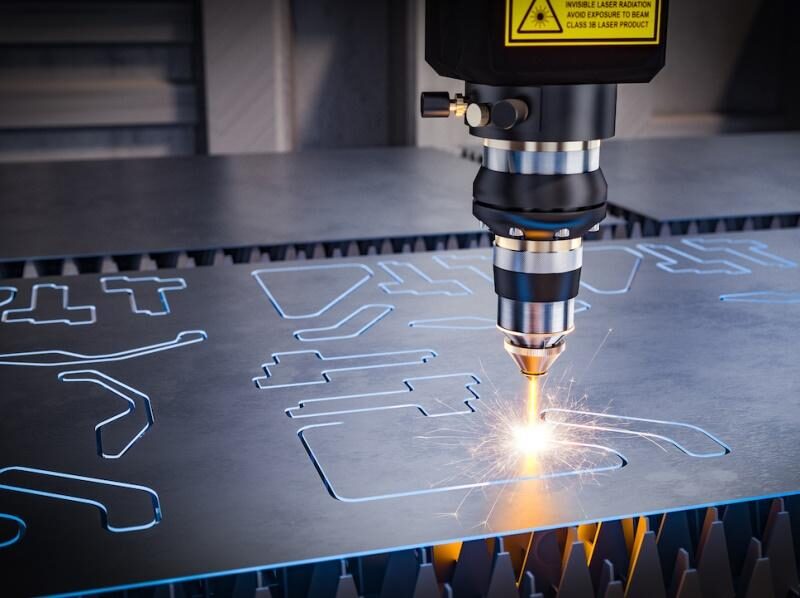
Quality Control in CNC Machining: Ensuring high standards
Introduction
In the precision-driven world of manufacturing, CNC (Computer Numerical Control) machining stands out as a cornerstone of modern production techniques. This process, which involves the use of computerized controls to manage complex machinery and tools, is pivotal in creating intricate parts with high accuracy and efficiency. However, the excellence of CNC machining isn’t just about the sophisticated technology or the skilled operators; it’s also heavily reliant on the stringent quality control measures that ensure each component meets the highest standards of precision and performance.
Quality control in CNC machining is not just a procedural step; it’s an integral part of the manufacturing ethos that dictates the success of the entire operation. From aerospace components to medical devices, the range of products relying on CNC machining is vast and varied, necessitating a robust approach to quality management. In this comprehensive guide, we will delve into the various facets of quality control in CNC machining, exploring how it helps in maintaining the impeccable standards demanded by diverse industries. We will examine the procedures, challenges, and future trends that shape this critical aspect of CNC machining, providing insights for both industry professionals and enthusiasts alike.
Understanding CNC Machining
CNC machining combines computer programming with mechanical process. The digital instructions, known as a program, guide the machine on how to accomplish a task. The versatility of CNC machining allows for producing a wide range of products, from simple bolts to aerospace components. The precision and repeatability of CNC machines make them indispensable in modern manufacturing.
Importance of Quality Control
Quality control in CNC machining isn’t just a step in the production process; it’s an integrated approach essential for the functionality and reliability of the final product. High-quality CNC parts are critical in industries like aerospace, automotive, and healthcare, where a minor defect can have significant consequences. Quality control ensures that every part meets strict standards, thereby reducing waste, saving time, and maintaining customer trust.
Quality Control Procedures
Pre-machining Inspections: Before machining starts, raw materials and machine setups are inspected. This includes checking material quality and ensuring machines are calibrated correctly.
In-process Quality Checks: During machining, operators and engineers monitor the process for any deviations. Modern CNC machines come equipped with sensors that provide real-time data, enabling immediate corrections.
Post-machining Inspections: After machining, parts undergo thorough inspections. This can involve visual inspections, dimensional checks using micrometers and calipers, and more sophisticated methods like Coordinate Measuring Machines (CMMs) and 3D scanning.
Technological Advancements in Quality Control
Advancements in technology have significantly enhanced quality control in CNC machining. Software solutions offer more precise control over machines, reducing the margin for error. Automated inspection technologies, like laser scanning and CMMs, provide faster and more accurate measurements. These technologies not only improve the quality of the products but also enhance the efficiency of the production process.
Automation and Robotics
Automation has been a game-changer in QC, offering speed and precision that human operators can’t match. Robotics, especially in repetitive and high-precision tasks, ensures consistent quality. Automated systems can work tirelessly, reducing human error and increasing throughput. In CNC machining, robots are now deployed for tasks like loading/unloading parts, which helps in maintaining consistent quality throughout the production process.
Advanced Imaging and 3D Scanning
3D scanning and advanced imaging technologies have revolutionized QC processes. High-resolution scanners and cameras capture detailed images of products from multiple angles, allowing for a thorough inspection. These images are then analyzed using sophisticated software that can detect even the minutest deviations from the desired specifications. This technology is particularly crucial in industries where precision is paramount, such as aerospace and medical devices.
AI and Machine Learning
Artificial Intelligence (AI) and Machine Learning (ML) are making significant inroads into QC. These technologies can analyze vast amounts of data from production processes to identify patterns, predict potential quality issues, and suggest improvements. AI algorithms can learn from every scan, improving their accuracy over time. This predictive quality control can help in identifying issues even before they occur, thereby reducing waste and increasing efficiency.
Internet of Things (IoT) and Big Data
The Internet of Things (IoT) interconnects machinery and devices, enabling real-time data collection and analysis. This interconnectedness, combined with Big Data analytics, provides a comprehensive overview of the manufacturing process. Manufacturers can monitor every aspect of production, from the condition of equipment to environmental factors, and make data-driven decisions to enhance quality.
Real-Time Monitoring and Feedback
Advancements in sensor technology allow for real-time monitoring of production processes. Sensors can track various parameters like temperature, pressure, and humidity, which affect product quality. Real-time feedback enables immediate adjustments, ensuring that the manufacturing process remains within the desired parameters, thus maintaining consistent quality.
Digital Twin Technology
Digital twin technology involves creating a virtual replica of a physical process or product. This virtual model can simulate how the real-world version would behave under different conditions. In QC, this means potential issues can be identified and rectified in the virtual model before the actual production, saving both time and resources.
Quality Control Software
The evolution of QC software has been integral in managing complex quality control systems. These software solutions offer enhanced data management, better visualization tools, and more efficient reporting mechanisms. They provide a platform for integrating various QC technologies, ensuring a seamless flow of information and enabling more informed decision-making.
Challenges in Quality Control
Despite advancements, challenges remain. These include dealing with complex part designs, ensuring consistency across batches, and maintaining the calibration of CNC machines. Addressing these challenges often requires a combination of skilled personnel, advanced technology, and continuous process improvement.
Complexity of Designs: Modern CNC machining often involves creating parts with complex geometries and tight tolerances. Managing the intricacies of such designs while maintaining high accuracy can be challenging. The more complex the part, the more difficult it is to inspect and ensure it meets all specifications.
Material Variability: The properties of raw materials can vary significantly, affecting the machining process and the quality of the final product. Factors like material hardness, grain structure, and thermal properties can influence the machining behavior. Ensuring consistent quality requires careful monitoring and adjustment of machining parameters.
Machine Calibration and Maintenance: CNC machines require regular calibration and maintenance to function at their best. Over time, machine components can wear, leading to deviations in accuracy. Keeping these machines perfectly calibrated is a constant challenge, especially in high-volume production environments.
Skill Level of Operators and Inspectors: The expertise of machine operators and quality inspectors plays a crucial role in quality control. Skilled personnel are needed to interpret complex designs, operate advanced machinery, and carry out precise measurements. A lack of adequately trained staff can lead to errors and inconsistencies in product quality.
Environmental Factors: External factors such as temperature fluctuations, humidity, and dust can affect both the machining process and measurement accuracy. Controlling the manufacturing environment is essential for maintaining consistent quality, especially in precision machining.
Integration of New Technologies: As CNC machining evolves, integrating new technologies (like advanced software, AI, and automation) into existing processes can be challenging. Adapting to these changes requires not only investment in new equipment but also training and a shift in operational procedures.
Quality Control Standardization: Ensuring that quality control procedures adhere to international standards (like ISO 9001) can be challenging, especially for smaller operations. Implementing these standards involves rigorous documentation, process standardization, and often, significant changes to existing practices.
Supply Chain Variabilities: Variabilities in the supply chain, such as inconsistencies in material quality or delays in material delivery, can significantly impact production schedules and part quality. Managing these variabilities requires robust supply chain management and contingency planning.
Balancing Speed and Quality: In a competitive market, there’s often pressure to increase production rates. Balancing the need for speed with the requirement for high-quality output is a constant challenge. Increasing production pace should not come at the cost of product quality.
Cost Management: Implementing comprehensive quality control measures can be costly. Investing in advanced inspection equipment, training personnel, and maintaining a controlled environment requires significant resources. Balancing cost while maintaining high-quality standards is a crucial challenge for many CNC machining operations.
These challenges highlight the need for a proactive and adaptive approach to quality control in CNC machining. Addressing these issues effectively requires a combination of skilled personnel, advanced technology, continuous training, and a commitment to continuous improvement. By overcoming these challenges, manufacturers can ensure the delivery of high-quality products, meeting both industry standards and customer expectations.
Best Practices in Quality Control
To achieve high standards in quality control, several best practices are recommended:
Regular Training: Continuous training for operators and quality control personnel ensures that they are up-to-date with the latest technologies and procedures.
Preventive Maintenance: Regular maintenance of CNC machines helps in avoiding unforeseen breakdowns and ensures consistent quality.
Continuous Improvement: Adopting principles like Lean manufacturing aids in continuously improving quality control processes.
Conclusion
Quality control is the cornerstone of successful CNC machining operations. As technology evolves, so does the approach to ensuring high standards. By understanding and implementing robust quality control procedures, embracing technological advancements, and preparing for future trends, manufacturers can ensure that CNC machining continues to be a reliable, precise, and efficient process in the manufacturing sector.