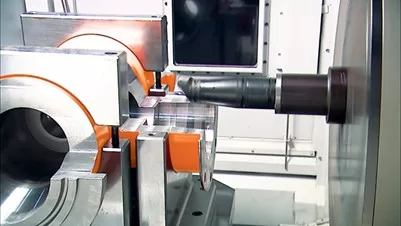
In the realm of modern manufacturing, Horizontal Machining Centers (HMCs) play a pivotal role in achieving precision, efficiency, and productivity. These advanced machining tools are essential for various industries, offering versatility and capability in producing complex components. However, maximizing the potential of HMCs requires expertise and strategic operation. In this guide, we present the top 10 tips for seamless HMC operations, ensuring optimal performance and output.
Common Mistakes Made by HMC Operators
Operating Horizontal Machining Centers (HMCs) requires precision, attention to detail, and thorough knowledge of the equipment. However, even experienced operators can fall into common pitfalls that compromise efficiency, productivity, and the quality of machined parts. In this section, we’ll explore some of the most prevalent mistakes made by HMC operators and provide insights on how to avoid them.
Neglecting Machine Maintenance
One of the most significant mistakes HMC operators can make is neglecting routine maintenance tasks. Failing to perform regular inspections, lubrication, and preventive maintenance can lead to accelerated wear and tear on critical machine components. This neglect not only compromises the accuracy and performance of the HMC but also increases the risk of unexpected breakdowns and costly downtime. Operators should adhere to manufacturer-recommended maintenance schedules and conduct thorough inspections to ensure the optimal functioning of the machine.
Ignoring Tool Wear and Breakage
Another common mistake is ignoring signs of tool wear or breakage during machining operations. Continuing to use dull or damaged cutting tools can result in poor surface finish, dimensional inaccuracies, and increased machining time. HMC operators should regularly inspect tools for signs of wear, such as chipping, edge rounding, or abnormal vibration. Implementing a tool management system that tracks tool life and automatically alerts operators to replace or recondition worn tools can help prevent costly errors and ensure consistent machining quality.
Overlooking Workpiece Setup and Fixturing
Proper workpiece setup and fixturing are essential for achieving accurate and repeatable machining results on an HMC. However, operators may overlook critical steps such as ensuring proper workpiece alignment, securing adequate clamping force, and verifying part orientation. Neglecting these aspects can lead to misaligned or improperly supported workpieces, resulting in scrapped parts or rework. To avoid this mistake, operators should carefully follow setup procedures, use appropriate workholding devices, and conduct thorough inspections before starting machining operations.
Inadequate Programming and Setup Verification
Inadequate programming and setup verification are common mistakes that can lead to costly errors and rework. HMC operators may overlook the importance of verifying CNC programs, tool offsets, and workpiece coordinates before initiating machining processes.
Poor Chip Management
Effective chip management is crucial for maintaining a clean and efficient machining environment on an HMC. However, operators may neglect to implement proper chip evacuation strategies, leading to chip buildup, tool damage, and surface finish issues. Failure to regularly clear chips from the work area, chip conveyor, and coolant system can result in machine downtime and reduced productivity. To avoid this mistake, operators should proactively monitor chip accumulation, use appropriate chip evacuation methods such as chip augers or conveyor systems, and regularly clean and maintain the machine’s coolant system.
Lack of Operator Training and Skill Development
Insufficient operator training and skill development can hinder the performance and capabilities of HMC operators. Operators who lack comprehensive training may struggle to optimize machining parameters, troubleshoot issues, and effectively utilize machine features and software tools. Without ongoing skill development, operators may also be unaware of best practices, new technologies, and advanced machining techniques that could enhance productivity and quality. To address this, companies should invest in continuous training programs that cover machine operation, programming, troubleshooting, and safety protocols to empower operators with the knowledge and skills needed to excel in their roles.
Failure to Optimize Cutting Parameters
Failure to optimize cutting parameters such as spindle speed, feed rate, and depth of cut is a common mistake that can impact machining efficiency and tool life. HMC operators may use default or conservative cutting parameters without considering the specific requirements of each machining operation. Suboptimal cutting parameters can result in excessive tool wear, poor chip control, and prolonged cycle times. Operators should conduct thorough cutting parameter optimization studies, taking into account factors such as material type, tool geometry, and workpiece characteristics to maximize machining efficiency and tool performance.
Inadequate Documentation and Record-Keeping
Inadequate documentation and record-keeping practices can lead to inefficiencies, errors, and difficulties in traceability and process improvement. HMC operators may fail to accurately document setup procedures, tooling changes, and machining parameters, making it challenging to reproduce successful setups or troubleshoot issues.
Solutions for HMC Operators
Invest in Proper Training
Effective operation of an HMC begins with comprehensive training for machine operators and technicians. Proper training ensures that personnel understand the machine’s capabilities, safety protocols, and maintenance procedures. By investing in training programs, you equip your team with the knowledge and skills necessary to operate HMCs proficiently, minimizing errors and maximizing productivity.
Optimize Tooling Selection
The selection of appropriate cutting tools is critical for achieving optimal machining results with an HMC. Consider factors such as material type, cutting speed, and feed rates when choosing tooling. Additionally, invest in high-quality tools and regularly inspect them for wear and damage. By optimizing tooling selection, you can enhance surface finish, prolong tool life, and minimize machining time.
Implement Efficient Workholding Solutions
Efficient workholding solutions are essential for securing workpieces during machining operations on an HMC. Utilize fixtures, vises, and clamping systems that provide stability, accuracy, and accessibility. Proper workholding reduces setup times, ensures consistent part positioning, and minimizes the risk of errors or rework. Experiment with different workholding techniques to find the optimal solution for your specific applications.
Maintain Machine Accuracy
Maintaining the accuracy and precision of an HMC is crucial for achieving reliable machining results. Regularly calibrate and inspect machine components such as linear guides, ball screws, and spindle alignment. Monitor thermal stability and implement measures to mitigate temperature fluctuations within the machining environment. By ensuring machine accuracy, you can uphold dimensional tolerances and produce high-quality components consistently.
Optimize Toolpath Strategies
Efficient toolpath strategies can significantly impact machining efficiency and cycle times on an HMC. Utilize CAM software to optimize toolpaths, minimize tool travel distances, and reduce air cutting. Implement strategies such as high-speed machining, trochoidal milling, and adaptive roughing to maximize material removal rates while preserving tool life. By optimizing toolpath strategies, you can streamline HMC operations and enhance overall productivity.
Implement Real-Time Monitoring
Real-time monitoring systems enable proactive maintenance and performance optimization for HMCs. Implement sensors and monitoring software to track vital parameters such as spindle load, tool wear, and coolant condition. Establish alarm thresholds to alert operators of potential issues or deviations from optimal conditions.
Ensure Proper Chip Management
Effective chip management is essential for maintaining a clean and efficient machining environment on an HMC. Implement chip evacuation systems such as chip conveyors, augers, or high-pressure coolant systems to remove chips from the work area. Regularly inspect and clean chip collection components to prevent chip buildup, which can lead to tool damage, poor surface finish, and machine downtime. Proper chip management ensures uninterrupted machining operations and prolongs tool life.
Implement Workpiece Probing
Workpiece probing systems enhance process control and accuracy by verifying part dimensions and alignment directly on the HMC. Integrate probing routines into machining programs to perform in-process measurements and compensate for variations in workpiece dimensions or fixturing. Utilize probing data to adjust tool offsets, optimize toolpath strategies, and ensure dimensional accuracy throughout the machining process. By implementing workpiece probing, you can reduce setup times, minimize scrap, and improve overall machining quality.
Optimize Coolant Delivery
Effective coolant delivery is critical for dissipating heat, lubricating cutting edges, and improving chip evacuation during machining on an HMC. Optimize coolant pressure, flow rate, and nozzle positioning to ensure thorough coverage of the cutting zone and efficient chip evacuation. Consider using programmable coolant nozzles or through-spindle coolant systems to deliver coolant precisely where it’s needed most. Regularly monitor coolant concentration and pH levels to maintain optimal coolant performance and prevent corrosion. By optimizing coolant delivery, you can enhance tool life, surface finish, and overall machining efficiency.
Embrace Continuous Improvement
Continuous improvement is fundamental to achieving excellence in HMC operations. Encourage a culture of innovation, experimentation, and collaboration within your machining team. Regularly review machining processes, analyze performance metrics, and identify opportunities for optimization or refinement. Implement feedback mechanisms to gather insights from machine operators, tooling specialists, and maintenance personnel. Embrace emerging technologies, industry best practices, and advancements in machining techniques to stay ahead of the competition. By embracing continuous improvement, you can drive innovation, boost productivity, and achieve sustainable growth in HMC operations.
Conclusion
Seamless operation of Horizontal Machining Centers (HMCs) requires a combination of expertise, strategic planning, and continuous improvement. By implementing the top 10 tips outlined in this guide, you can optimize HMC performance, maximize productivity, and achieve superior machining results. Invest in training, optimize tooling and workholding, maintain machine accuracy, and embrace technology-driven solutions to unlock the full potential of HMC operations. With a focus on efficiency, precision, and innovation, your organization can excel in the competitive landscape of modern manufacturing.